ROBOTIC WELDING CELLS
A robotic welding system is an advanced industrial automation solution designed to perform welding processes in a fully automated manner.
These systems combine robotic arms, welding equipment, and digital control systems to ensure precision, speed, and repeatability in joining metallic materials.
MAIN FEATURES
- Robotic Arm:
A programmable mechanical element that executes the necessary welding movements, following predefined paths with high precision. - Welding Sources:
Includes technologies such as MIG (Metal Inert Gas), TIG (Tungsten Inert Gas), or resistance welding, depending on production requirements. - Feeding Systems:
Provide a continuous and controlled supply of consumables such as welding wire, shielding gas, and electrical current. - Control Software:
A digital interface that allows programming welding parameters (speed, power, joint type) and monitoring the entire process in real time. - Sensors and Cameras:
Used to detect positioning, make real-time adjustments, and correct deviations during the process.
ADVANTAGES
- High Precision:
Eliminates human errors and ensures uniform joints. - Increased Productivity:
Operates continuously and quickly, reducing production times. - Cost Reduction:
Minimizes material waste and optimizes resources. - Safety:
Reduces operator exposure to risks related to fumes, heat, and sparks.
APPLICATIONS
Automotive
Frame and metal component joints
Aerospace sector
Precision welding
Metal carpentry
Load-bearing structures
Household components
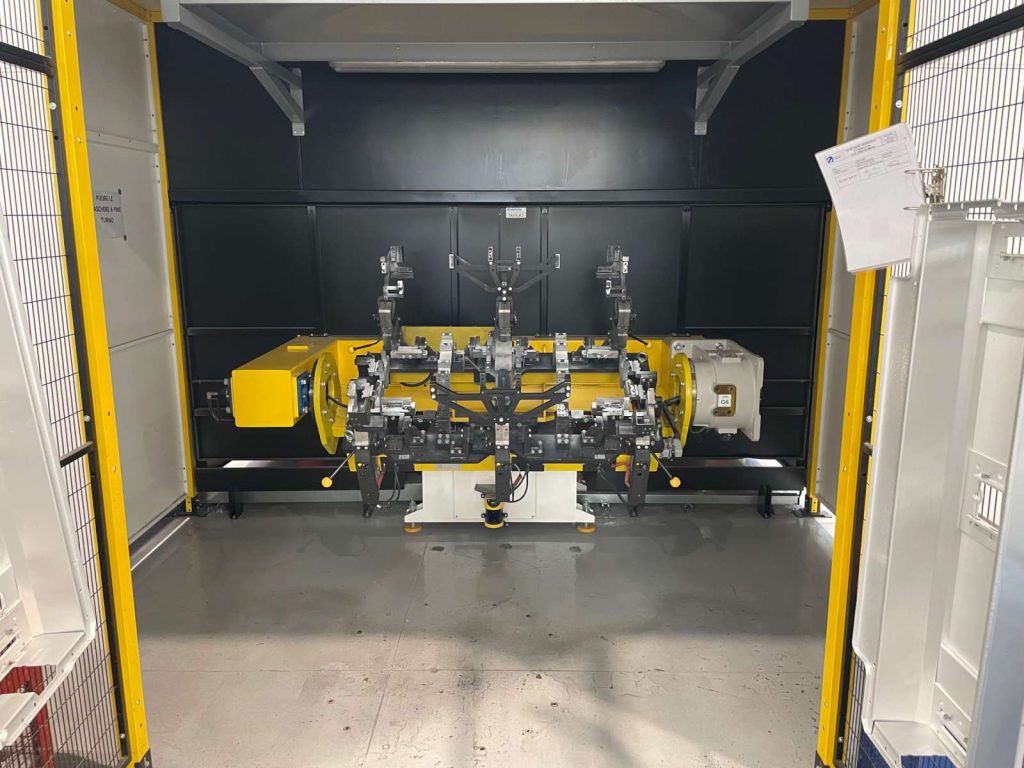
In summary, a robotic welding system is an ideal solution for companies looking to enhance production efficiency and product quality, with a focus on technological innovation and sustainability.